If you’ve kept abreast with the news, Autodesk’s Product Design and Manufacturing Collection now ships with Nastran In-CAD. For FEA fanatics such as myself, this is fantastic news. Nastran enjoys a solid reputation in the industry of engineering analysis and for good reason. But how is it different from Inventor’s native FEA offering, Stress Analysis? Read on to learn a little more about these tools, and see how they compare!
Old Faithful: Inventor’s native Stress Analysis
Inventor’s native Stress Analysis tool is an absolutely awesome workhorse. While it is quite limited in terms of the materials and analyses it can work with, not all problems require hyper-powerful tools. For the right problems, it more than makes up for its limitations with its splendid UI and workflow, being slick, quick and easy to use – so much so that I often see this used as the go-to for quick design checks. As an added bonus, because it was built right into Inventor from the start, Stress Analysis is able to leverage model parameters in order to drive design optimisation studies quickly and easily – useful for things like optimising the diameter of a connection pin.
Pros
– Easy to learn,
– Easy to use,
– Quick,
– Accurate for non-extreme load cases,
– Capable of parameter-driven optimisation studies.
Cons
– Studies limited to Linear Static and Modal Analysis,
– Materials may only be linear metals with simple characteristics,
– Boundary condition definitions are relatively simple (mechanical).
NASTRAN In-CAD
Developed for NASA in the 1960’s, NASTRAN has been around for quite a while, being continually developed and polished into one of the most powerful and trusted FEA packages today. Thanks to the magic of acquisition, NASTRAN now exists as a plug-in for Inventor (“NASTRAN In-CAD”), accessible from the Environments tab.
Counter to Inventor’s native Stress Analysis, NASTRAN is complex and a bit more difficult to use, but also far more powerful and comprehensive. Able to deal with a multitude of study types and materials (see tables below), it is definitely the cavalry when it comes to FEA.
Pros
– Wide variety of study types, including non-linear, transient and thermal,
– Wide variety of materials, including metals, plastics, ceramics, etc. with linear, non-linear, fatigue, anisotropic and laminate properties considered.
– Accurate for a wide array of load cases, including extreme loading,
– Capable of complex boundary conditions (mechanical, thermal, transitional).
Cons
– Workflow is more complicated,
– Not yet capable of parameter-driven optimisation.
Side-by-side Comparison
Tabulated below are side-by-side comparisons of the two FEA tools with regard to their offered types of analysis and their available materials.

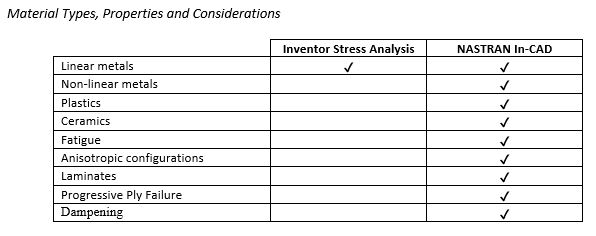
Conclusions
Personally, while I would love to say that I will still use the old workhorse that is Inventor’s native Stress Analysis tool, I am too excited not to run everything through NASTRAN In-CAD. The last few years have seen incredible polish applied to NASTRAN’s UI, and today, it is a pleasure to use and as powerful as ever; an extremely welcome addition to the Autodesk family.
For more information on this blog post or if you have any other questions/requirements, please complete the below form:
Related Links
Autodesk Inventor – Autodesk Platinum Partner | Man and Machine
Simulation Services – Inventor Nastran – FEA | Man and Machine
Autodesk Inventor Training Courses | Man and Machine
Simulation Training – Autodesk Inventor & Moldflow | Man and Machine